Новости

Специалисты Главного управления ОАО «ТГК-2» по Вологодской области устранили все дефекты, выявленные в ходе гидравлических испытаний на магистральных теплотрассах, и в ходе ремонтных работ заменили более 400 метров аварийных участков. В ближайший месяц теплоэнергетики завершат последний этап подготовки трубопроводов и оборудования Вологодской ТЭЦ к предстоящему отопительному сезону.
По итогам опрессовки на теплосетях Центрального района города было обнаружено 21 повреждение, Южного района - 7 прорывов. Причиной возникновения дефектов является общий износ теплосетевого комплекса, составляющий порядка 50%. В целях обновления тепловых сетей и обеспечения качественной подачи тепла потребителям Центральной части Вологды специалисты Компании реконструируют тепломагистраль с заменой головного участка большого диаметра общей протяженностью 1 км в однотрубном исчислении.
- Ежегодно в ходе летних ремонтов мы обновляем теплотрассы, а также трубопроводную арматуру, чтобы уменьшить потери при передаче тепловой энергии по сетям и улучшить качество энергоснабжения потребителей. Параллельно с этим идет ремонт основного и вспомогательного оборудования Вологодской ТЭЦ. Так, для повышения уровня промышленной безопасности энергооборудования станции до конца сентября мы проведем реконструкцию обвязки газовых горелок на паровом котле.№5 с установкой современной системы "АМАКС", - говорит главный инженер Вологодского управления ТГК-2 Михаил Рыбин.
Большая часть оборудования на Вологодской ТЭЦ уже отремонтирована, осталось до 10 октября выполнить плановые ремонты энергетического котла №6 и водогрейного котла №3. Таким образом, ремонтная кампания на станции и тепловых сетях будет завершена до начала отопительного сезона.
Справка:
«Территориальная генерирующая компания №2» создана в апреле 2005 года. ТГК-2 является одной из крупнейших теплоэнергетических компаний Севера и Северо-Запада России. Генеральный директор ОАО «ТГК-2» – Владлен Александрович. Компания занимается производством и реализацией электрической и тепловой энергии. Предприятия ТГК-2 расположены в Архангельской, Вологодской, Костромской, Новгородской, Тверской и Ярославской областях.
Под управлением Компании находятся 16 ТЭЦ, 10 котельных, 4 предприятия тепловых сетей (без учета арендованного имущества). Общая установленная электрическая мощность предприятий ТГК-2 – 2541,5 МВт, установленная тепловая мощность – 11079,833 Гкал/час.

ОАО «Газпромнефть - Московский НПЗ» извещает о проведении открытого отбора организации, способной разработать рабочую документацию по монтажу трубопроводной арматуры на установках ОАО «Газпромнефть - МНПЗ».
Дата и время окончания приема заявок – 12 сентября 2012 г. в 16 часов 00 минут (время местное, г. Москва).
Организатор отбора проведет процедуру их публичного вскрытия 13 сентября 2012 г. в 11 часов 00 минут (время местное, г. Москва). Контактная информация по любым вопросам, касающимся организации и проведения отбора – тел.: 8 (495) 734-93-58; 8 (495) 734-92-00, доб. 28-17, электронный адрес: lemeshev.ak@mnpz.ru.
Более подробную информацию о конкурсе можно найти здесь
Справка:
«Газпромнефть – Московский НПЗ» - нефтеперерабатывающее предприятие компании «Газпром нефть» по итогам 2011 года входит в число 10-ти наиболее эффективных НПЗ России. Завод занимает ведущие позиции в производстве высокооктановых бензинов и дизельных топлив, обеспечивая порядка 40% потребностей Московского региона в нефтепродуктах.
Установленная мощность ОАО «Газпромнефть-МНПЗ» составляет 12, 15 млн тонн нефти в год. В 2011 году на Московском НПЗ было переработано 10,8 млн тонн нефти – это на 6% превышает результат 2010 года. Глубина переработки по итогам года составила 72,3 % , выход светлых нефтепродуктов – 6,1 млн тонн, в том числе 2,2 млн тонн высокооктановых бензинов, что на 9,6 % превышает показатели аналогичного периода прошлого года. В 2011 году завод также произвел 2,6 млн тонн дизельного топлива и 649 тыс. тонн авиакеросина.
В 2010 году Московский НПЗ был интегрирован в структуру группы компании «Газпром нефть». В настоящее время на Московском НПЗ реализуется первый этап программы по реконструкции и модернизации мощностей, направленный на улучшение качества производимой продукции. Программа модернизации Московского НПЗ предусматривает доведение технологий и качества производимых на предприятии нефтепродуктов до уровня мировых стандартов. Объем инвестиций, которые «Газпром нефть» планирует направить на развитие завода до 2020 года, составит порядка 130 млрд. руб.
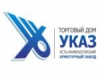
Усть-Каменогорский арматурный завод (УКАЗ) продолжает масштабную программу модернизации, в рамках которой предполагается приобретение оборудования на сумму более 50 млн $. В настоящий момент полным ходом идет второй этап перевооружения предприятия.
21 августа 2012 года на УКАЗе введен в эксплуатацию фрезерно-расточной станок модели FT45TG итальянской фирмы “ALESAMONTI” с числовым программным управлением стоимостью более 1.5 млн евро.
Данное оборудование позволяет осуществлять скоростную силовую механическую обработку тяжелых деталей с высокой точностью. При этом производительность обработки возрастает более чем в 4 раза, поскольку 1 итальянский станок способен заменить около 4 единиц устаревшего оборудования.
Для работы на новом оборудовании необходима высокая квалификация специалистов, поэтому в контракте с компанией - производителем предусмотрено обучение персонала предприятия.
«Обновление оборудования механического участка - один из этапов комплексной программы по модернизации завода «УКАЗ»,- комментирует генеральный директор АО «УКАЗ» Эрнест Мюллер. – В этом году мы приступили ко второму этапу программы модернизации, стартовавшей в 2010 году. Его реализация позволит увеличить производительность предприятия более чем на 40 %».
Справка:
АО «Усть-Каменогорский арматурный завод» более 35 лет проектирует, разрабатывает, производит и осуществляет поставку трубопроводной арматуры и нефтегазопромыслового оборудования, которые находят широкое применение на нефтегазовых объектах России, государств СНГ, а также в странах дальнего зарубежья.
Продукция изготавливается в соответствии со стандартами Российской Федерации и Республики Казахстан, и ее качество подтверждено необходимыми разрешениями и сертификатами соответствия.
На предприятии внедрена и сертифицирована система менеджмента, одобренная компанией Lloyd’s Register Quality Assurance. Она включает в себя систему качества, систему экологического менеджмента, систему охраны труда и промышленной безопасности по международным стандартам ISO 9001, IS014001 и OHSAS 18001. Официальным и полномочным представителем АО «Усть-каменогорский арматурный завод является Торговый Дом «УКАЗ», офис которого находится в Москве.

ЗАО «Энергомаш (Белгород) – БЗЭМ» обращает особое внимание специалистов эксплуатирующих, строительно-монтажных и проектных организаций на имеющиеся факты мошенничества со стороны поставщиков сильфонных компенсаторов, при которых поставляются компенсаторы с несоблюдением проектного требования отсутствия передачи распорного усилия на трубопровод и оборудование.
Недобросовестные поставщики предоставляют заказчику сравнительно низкие цены на продукцию, обещают невероятно короткие сроки поставки, гарантируют качество изделий и полное их соответствие требованиям заказчика. Казалось бы, все условия взаимовыгодного сотрудничества соблюдены…
Но, после поставки изделия на объект или, что еще хуже, после монтажа, а иногда даже на стадии испытаний, выясняется, что вместо компенсаторов, не передающих распорное усилие на трубопровод (таких как разгруженные, сдвиговые, угловые, карданные), поставляются обычные универсальные компенсаторы, передающие распорное усилие на трубопровод, не имеющие необходимых стяжек, шарниров, опорных колец и прочих усиливающих и ограничивающих элементов. Не чистые на руку поставщики ввиду низкой инженерно-технической компетенции либо намеренного игнорирования особенностей проекта заказчика, поставляют простые в изготовлении, и потому дешевые, универсальные сильфонные компенсаторы, представляющие собой лишь слегка усиленные версии обычных осевых компенсаторов.
Самые тяжкие последствия наступают, в случае если подлог вскрывается уже после монтажа или даже на стадии испытаний, когда трубопровод и дорогостоящее оборудование, которое в соответствии с проектом должен был бы защищать сильфонный компенсатор, не передающий распорное усилие на трубопровод, выходит из строя и приводит к разрушениям, и даже, не дай Бог, к человеческим жертвам. Попавшие в ловушку низких цен и коротких сроков поставки заказчики, вынуждены повторно заказывать уже соответствующую проекту продукцию, теряя денежные средства, время, зачастую срывая сроки монтажа и ввода в эксплуатацию подведомственного объекта.
Рекомендуется при анализе предложений различных поставщиков в первую очередь быть очень внимательными при закупке не предусмотренных проектом изделий. В отношении же технических характеристик лучше сравнивать не только строительную длину, габаритный диаметр, величину рабочего хода, жесткость, количество слоев в сильфоне, циклику, массу компенсаторов, но и обращать особое внимание на наиважнейший параметр – передает ли устройство распорное усилие на трубопровод.
Такой всесторонний подход не только сэкономит время на реализацию проекта и денежные средства, но и позволит избежать техногенных катастроф и человеческих жертв.
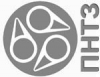
На Первоуральском новотрубном заводе (входит в компанию ЧТПЗ) завершены крупномасштабные работы по ремонту трубопрокатного стана "140-1", производящего бесшовные горячекатаные трубы диаметром 57-133 мм общего и специального назначения из различных марок стали.
В ходе капитального ремонта восстановлен геометрический размер клети прошивного стана и ее составляющих, изготовлены и заменены уникальные крупногабаритные детали прошивного стана: выходные рамы обкатных машин и параллели. Кроме того, на участке подготовки трубной заготовки проведена ревизия всех механических узлов пресса для ломки заготовки, заменены сортировочный стол и стол загрузки, восстановлена система транспортизации. В методической печи стана заменена кладка стен, падины, свода; полностью восстановлены металлоконструкции, загрузочные столы и выходной желоб.
Результатом осуществленных мероприятий станет бесперебойная работа трубопрокатного стана, улучшение потребительских свойств продукции, увеличение объемов производства. Мощность стана в ходе ремонта не изменилась, она составляет 100 тысяч тонн трубной продукции в год. Ежемесячно стан "140-1" выпускает порядка 6 тысяч тонн готовой трубной продукции и 1,5 тысячи тонн полуфабрикатов для волочильных цехов и Финишного центра ПНТЗ.
Справка:
Первоуральский новотрубный завод является ведущим предприятием России и Европы по выпуску стальных труб. За годы своего существования завод вобрал в себя передовой производственный опыт ведущих зарубежных и отечественных предприятий. В технологических процессах применяется передовое оборудование, изготовленное известными заводами России, Германии, США, Италии, Великобритании, Швейцарии.
|